各国の規制強化やESG投資、コロナ禍で注目されるグリーンリカバリーも追い風となって、世界の電動自動車(EV)へのシフトが加速しています。ただ現実的にEVが普及するには、燃(電)費や耐久性をもっと高め、「航続距離」を伸ばすことが求められます。そこで期待されているのが、樹脂材料の活用です。旭化成には、さまざまな特性をもつ高機能樹脂(エンジニアリングプラスチック、以下「エンプラ」)のラインナップがありますが、それらは実際どのような貢献ができるのでしょうか。EVを取り巻く現状と未来を展望しながら、パフォーマンスプロダクツ事業本部の安西克夫と大池慎太郎に話を聞きます。
旭化成の製品や活用方法に関するお問い合わせはこちらのフォームよりご連絡ください。
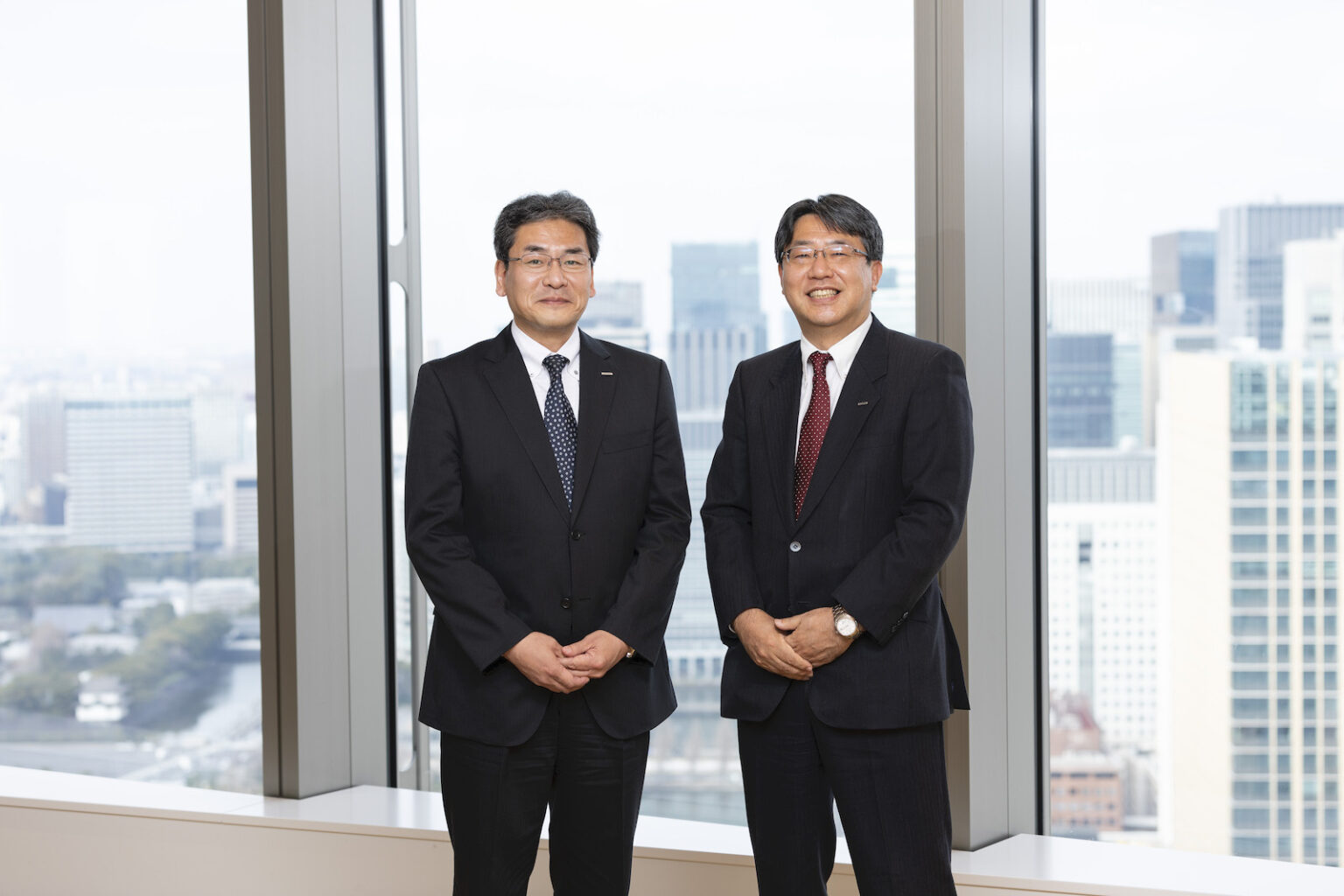
▲パフォーマンスプロダクツ事業本部 モビリティマテリアル事業部長 安西克夫(右)、同本部 企画管理部 モビリティマテリアル企画室長 大池慎太郎(左)
EVへのシフトは、想定の3倍速以上で進んでいる
大池「航続距離について入る前に、自動車産業の枠組みが従来からだいぶ変わってきている現状をお話ししたいと思います。パワートレイン(動力源)別の自動車生産台数について、2017年9月時点での予想と2021年2月の予想<下記グラフ①②>を比べると、わずか3年強で、2030年の赤の部分BEVの予想台数が約3倍に増えていることがわかります。BEVとはバッテリーのみの電動自動車のことで、以下EVと言う時はBEVのことを指します。ハイブリッド車(HV)はエンジンを搭載しているので、BEVではありません。さらに私たちモビリティマテリアル事業部の見立てとしては、燃料電池車(FCV)も含め電動化への移行は、②の予想よりもっと進むと見ております」
EVバッテリーはエンジンより圧倒的に重い
大池「もう一つ、航続距離についてお話しする上で前提になるのは、EVとガソリン車(ICE)の重量の違いがあります。EVとICEを、軽自動車・小型車・セダン・高級車といった車格の同じものどうしで比べた場合、どの車格もEVの方が現状では重いです。ガソリンエンジンは大体100kg〜200kg前後ですが、バッテリーは250kg〜600kg前後が一般的。この重量差によって、車体重量が決定的に変わってきます」
走行距離と耐久性、両方の航続距離を伸ばしたい
安西「これらのことが大前提として本題に入りますが、航続距離には一回の充電で走れる距離の長さと、車一台あたりのトータルで走れる距離の長さ、いわゆる耐久性という二つの意味合いがあります」
大池「一回の充電で考えると、今一般的なICEだと東京〜大阪間(約500km)は給油しないで走れるという状態なのに対して、EVの一般的な車では、走行以外にも例えばエアコンやオーディオ等、電力を使う機能があるため、途中で充電が必要になることがあります。充電設備などインフラがまだ整っていないですし、充電するにもガソリンの補充と比べて時間がかかります。容量を増やそうとバッテリーを大きくすれば重くなり、燃費――EVの場合“電費”と言うのですが、重いものを動かせば電費を食うので、思うように航続距離が伸びないというジレンマに陥ります」
安西「耐久性で考えると、EVの電池はまだまだ劣化しやすく、長持ちしません。EVの普及には走行距離と耐久性、両方を考慮した上で航続距離を長くすることが求められています。航続距離が長くなると、車の価値向上につながります」
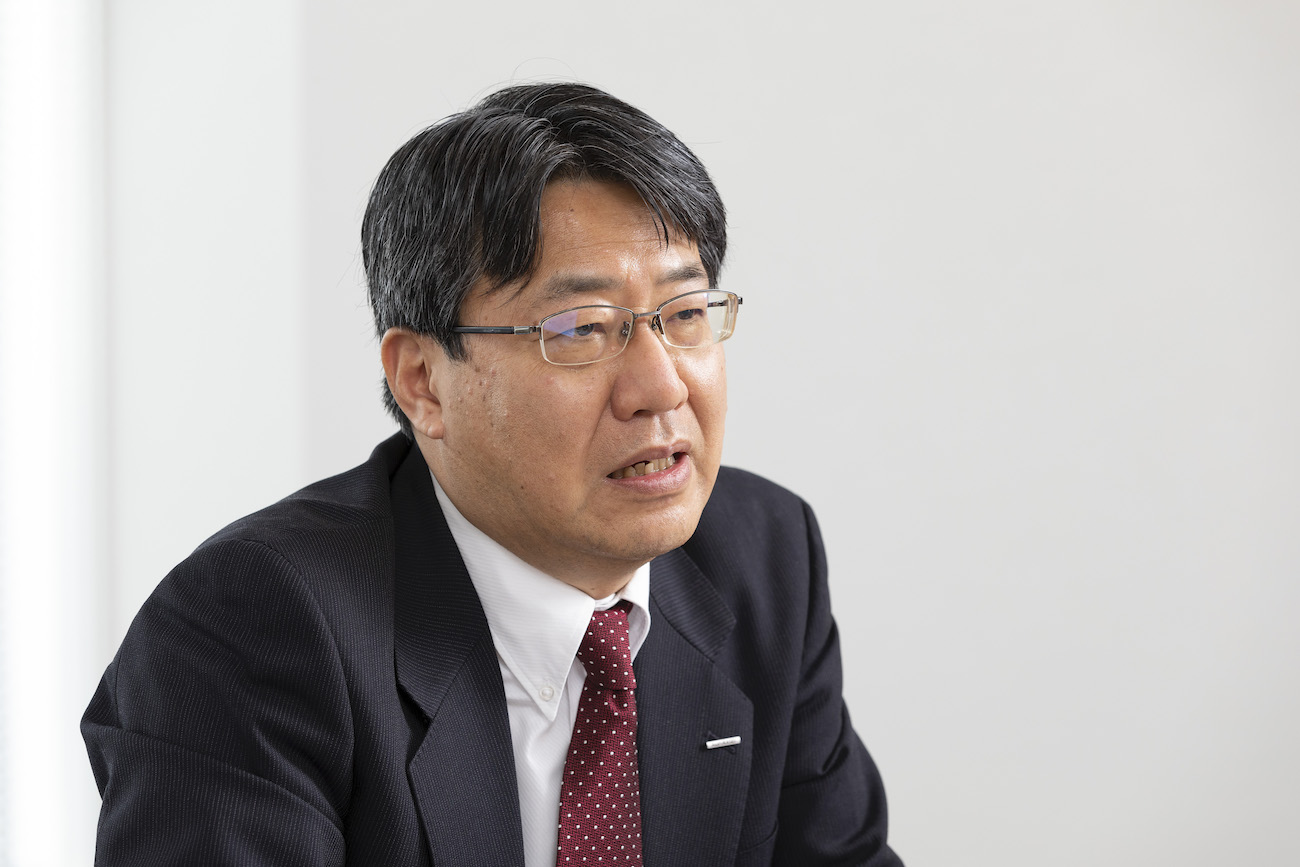
▲パフォーマンスプロダクツ事業本部 モビリティマテリアル事業部長 安西克夫
旭化成は“軽量化”と“熱マネジメント”で貢献できる
大池「航続距離を伸ばすために重要なのは、重量・バッテリー効率・タイヤの転がり抵抗・ギアの変速効率・ボディの空気抵抗・駆動効率などさまざまな要因があります。あの手この手で対策が取られていますが、私たち樹脂メーカーとしては、車体の『軽量化』とバッテリーの『熱マネジメント』で貢献できると思います」
◆ “軽量化”はトータルで航続距離を伸ばす
大池「私たちが『樹脂化』という言葉を使うときは、金属から樹脂に替えることを意味します。鉄から樹脂化すると、鉄の比重は7.8、樹脂はだいたい1.3〜1.4なので単純比較で5分の1から6分の1に軽量化できます。アルミの比重が2.7なので、アルミと比べてもだいぶ軽量化できます。
車体を軽量化すると、空気抵抗・加速抵抗・転がり抵抗・勾配抵抗といった全ての走行抵抗が減って、オールマイティに電費効率が良くなります。約1トン超の小型車のボディで100kg軽量化できると、一般論ですが1リッターあたり1km燃費が良くなり、CO2排出量が1kmあたり15g減らせます。環境規制のために軽量化する効果は大きいため、例えばアメリカでは、自動車生産に使用される材料のうち比重の重い鉄の占める割合が、2015年に8割近くあったのがどんどん下がってきています」
◆バッテリーを“熱マネジメント”して耐久性の航続距離を伸ばす
大池「EVに使われるリチウムイオンバッテリー電池には、最適な環境温度というのがあって、それよりも低温でも高温状態でも本来の性能を発揮することができません。バッテリー周辺部材を断熱性、保温性に優れた樹脂にして適温に熱マネジメントすれば、バッテリーはより高い能力を発揮して効率良く使うことができ、電池寿命が長くなって耐久性を上げることに繋がります」
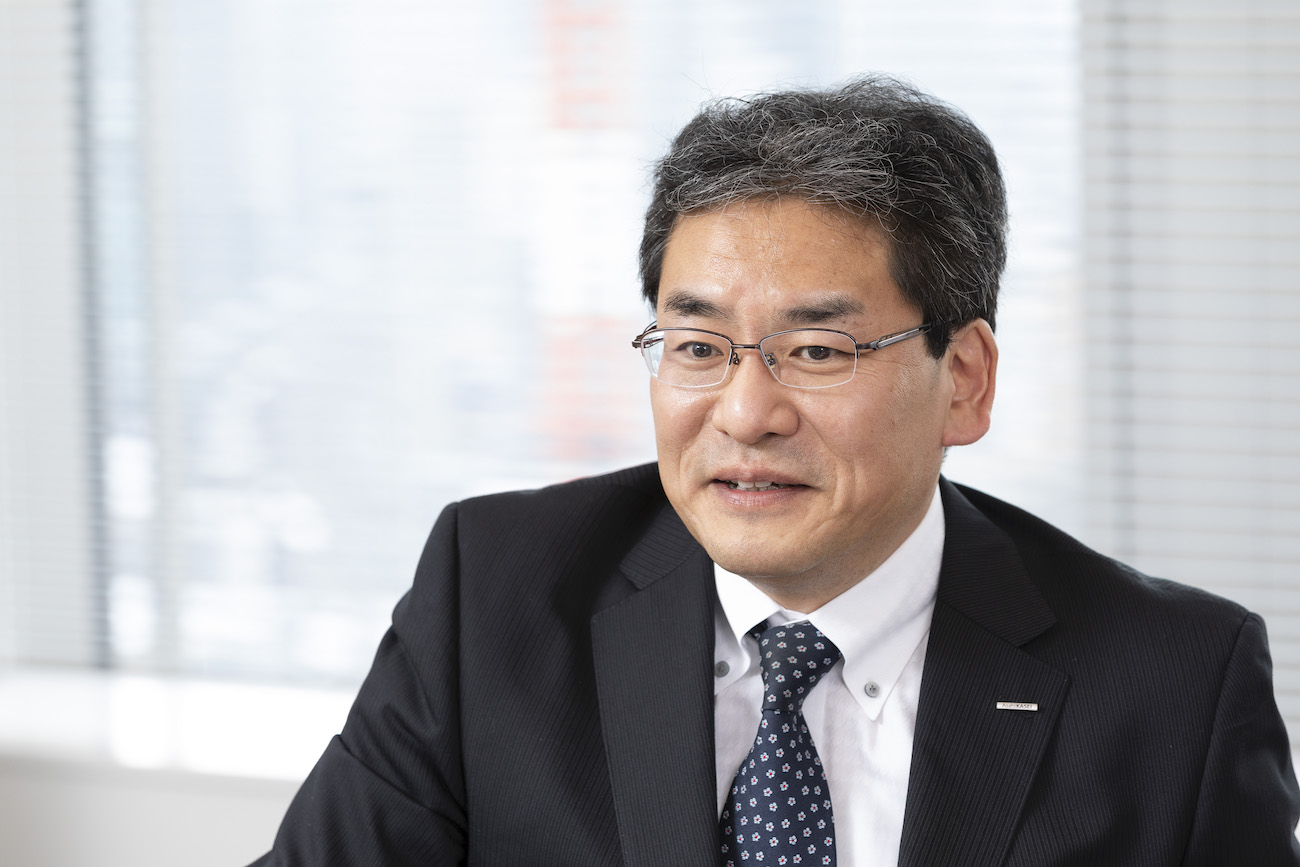
▲パフォーマンスプロダクツ事業本部 企画管理部 モビリティマテリアル企画室長 大池慎太郎
二つの航続距離を伸ばす、旭化成のエンプラとは…
安西「私たちの身近なところにあるレジ袋などの“汎用樹脂”とは、耐熱温度や機械的な強さ剛性、対薬品性などでレベルが違う樹脂を“エンジニアプラスチック”、略して“エンプラ”と呼んでいます。旭化成は3種類のエンプラ『ザイロン』『レオナ』『テナック』を持っていて、さまざまな軽量化に取り組んできました。これらを原料に、さらに加工して開発した新しい素材として『サンフォース』と『連続繊維(連続ガラス繊維強化ポリアミド樹脂)』があります」
◆実績を重ね、実力を磨いてきた旭化成のエンプラ3兄弟
大池「例えばバッテリーケースは従来かなり大きな金属の塊でした。そのいくつかのパーツを『ザイロン』で樹脂化するだけでキロ単位の軽量化ができます。断熱性や保温性といったバリア性も高いので、熱マネジメントに優れ、電池寿命が長くなります」
●ザイロンTM https://asahi-kasei-mobility.com/products/xyron/
活用例:バッテリーパック(ケース)、リレーブロック、セルセパレーター(電池部材)、フェンダー、ホイールキャップなど外装パーツなど
大池「熱マネジメントで重要な水冷式の冷却パイプは数メートルに渡る長さがあり、『レオナ』で樹脂化すると大幅に軽量化できます。腐食性防止や保温性にも優れています」
●レオナTM https://asahi-kasei-mobility.com/products/leona_sv104/
活用例:高電圧タイプのケーブル、水冷式冷却パイプ、トランスミッション周辺機器、シフトレバー、シリンダーヘッドカバー、ミラーベース、カップホルダーなど
大池「『テナック』は非常に強靭、かつ摺動(しゅうどう)性つまり滑りのいいエンプラで、ギアなどに多く活用されています。意匠性を兼ね備えたラインナップもあります」
●テナックTM https://asahi-kasei-mobility.com/products/tenac/
活用例:ギアの部品、インサイド(扉の内側)ハンドル、シートベルトプレスボタン、ワイパーギアユニット、ウィンドウレギュレーター部品など
◆注目の新素材!発泡体で強い「サンフォース」、薄く頑丈な「連続繊維」
安西「『サンフォース』は、発泡させて5倍から10倍に膨らませたエンプラです。非常に軽く、いろいろな形に成形できます。強度・剛性が高く、難燃性、耐熱性、断熱性に優れ、寸法精度も高いので、電池まわりのような熱マネジメントに関わる部材や芯材として貢献できます」
●サンフォース®️ https://asahi-kasei-mobility.com/products/sunforce_bebh/
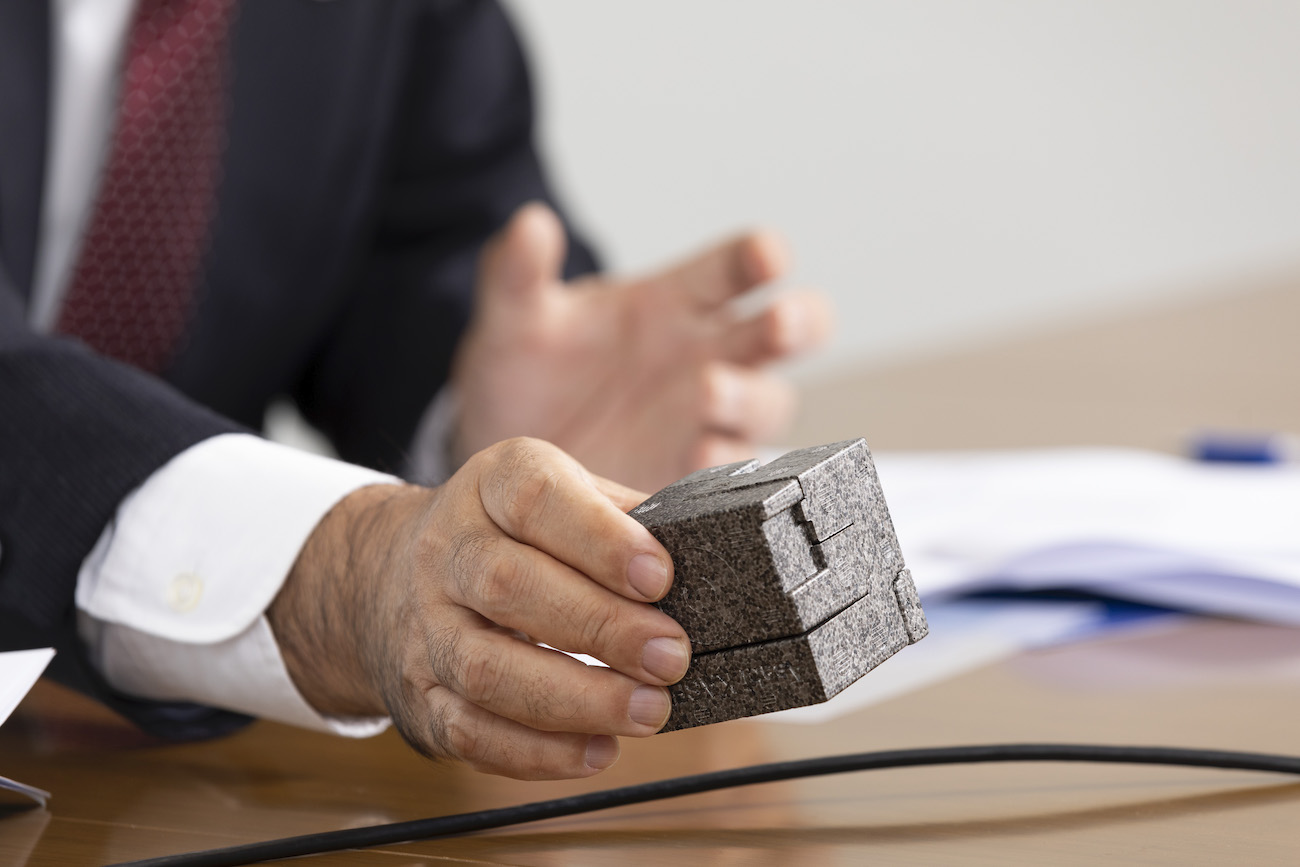
▲ブロック状に加工し、彩色された「サンフォース」。手に持ってみると非常に軽いことがわかる。
安西「『連続繊維』は、エンプラにガラスファイバー長繊維の織物を組み合わせた最新の素材です。ガラスの織物はものすごく強度が高く、衝突安全性に優れたコンポジットなので、車体の構造部材などさまざまな部位での採用が期待されています。シート状に作られ、お客様のところで部品の形に加工していただきます」
●連続繊維(連続ガラス繊維強化ポリアミド樹脂) https://asahi-kasei-mobility.com/products/continuous_glass_fiber/
樹脂化によるコストダウンでEV開発を後押しする
大池「樹脂化することは、軽量化と熱マネジメントによって航続距離を伸ばすだけでなく、トータルコストダウンにも繋がります。さまざまな部品を樹脂化することで、例えば金属並みの安全性や意匠性をより安く提供できます。樹脂は複雑な形状も成形できるので、部品と部品を複合化、一体化して部品数を減らしたり、小さくすることもできます。部品が減れば工場での組み付け時間が短縮できますし、部品が小さくなれば省スペースになり、設計の自由度が向上します。私たちが貢献できるところをどれだけ見つけるかというのが、旭化成のエンプラの自動車向け材料開発、用途開発の肝になってくると思います」
プロダクトとソリューションの両方から提案力を高めていく
安西「自動車業界が大きく変わりつつある中で、私たちの開発スピードもさらに高めていくことが必要とされています。従来は、私たちのエンプラ素材を使った部品をTier1(部品一次メーカー)さんに作ってもらってから自動車メーカーさんに紹介してーーという流れでしたが、最近では自動車メーカーさんと私たち材料メーカーとの協業を求められているところもあります。
今あるエンプラによる樹脂化をご提案するだけでなく、新しい素材の開発と、従来のエンプラとの複合化にも注力していきたいと思っています。新しい素材は、使い方や使うとどのような価値が生まれるのかをわかりやすくお示しする必要があるので、CAE(コンピュータを使ったシミュレーション技術)によるご提案も行っています。製品を作るプロダクトアウトと、ソリューションの両面を高めて、より新しいニーズをキャッチして対応し、モビリティ関連のビジネスの拡大を図っていきたいと思っています」
激動するフィールドで、モチベーション高く挑戦していく
大池「EV化を進める国々にはそれぞれ事情があって、特にヨーロッパがEVに一気に舵を切った背景には、ディーゼル車の排ガス規制でのつまずきや、国によって再生可能エネルギーの利用が進んでいたり、電力コストが安かったりすることが挙げられます。一方で、今一番EVが成長しているエリアは中国です。私たちモビリティマテリアル事業部は、自動車技術の先端地域であるヨーロッパのトレンドを意識しながら、中国などの成長市場をターゲットにしています」
未知数の未来に、いかに先んじて対応していけるか
安西「EVが全て最良というわけではなく、FCVのように燃料電池も可能性が高いと考えていますが、まだまだコストが高過ぎます。世界的にEVが拡大するのは間違いないと思っていますけれど、どこまでどうなっていくのかはまだまだ不透明な部分もあり、いかに先んじて対応していけるかが各社の勝負だと思います。新しい素材を中心とした新たな価値創造へのチャレンジは、外部環境とくに自動車の世界が激変しつつある中で、取り組み甲斐がありますね」
各素材についての詳細情報
『旭化成 エンジニアリングプラスチック総合情報サイト』
https://www.asahi-kasei-plastics.com/
旭化成の製品や活用方法に関するお問い合わせはこちらのフォームよりご連絡ください。
この記事は2021年5月7日に公開しました。