Going the Distance
Weight reduction and thermal management to extend the driving range of electric vehicles
-Case: High performance plastics with SunForceTM foam beads and flame-retardant XYRONTM
May 7, 2021
Recently, the shift to electric vehicles (EVs) in the global automotive industry is accelerating due to tightening regulations, ESG investments, and the global COVID-19 pandemic. However, to make EVs adopted on a global scale, automakers must further extend their driving range by improving mileage (reducing electricity costs) and durability. To achieve this, carmakers intend to use more plastics materials and Asahi Kasei is here to lend a hand with an extensive lineup of versatile engineering plastics. Though, how can plastics actually contribute to improving a vehicle’s driving range? We will talk with Katsuo Anzai and Shintaro Oike from the Performance Products SBU about the status quo and the future of EVs.
Click here to contact us about Asahi Kasei’s products and usage examples.
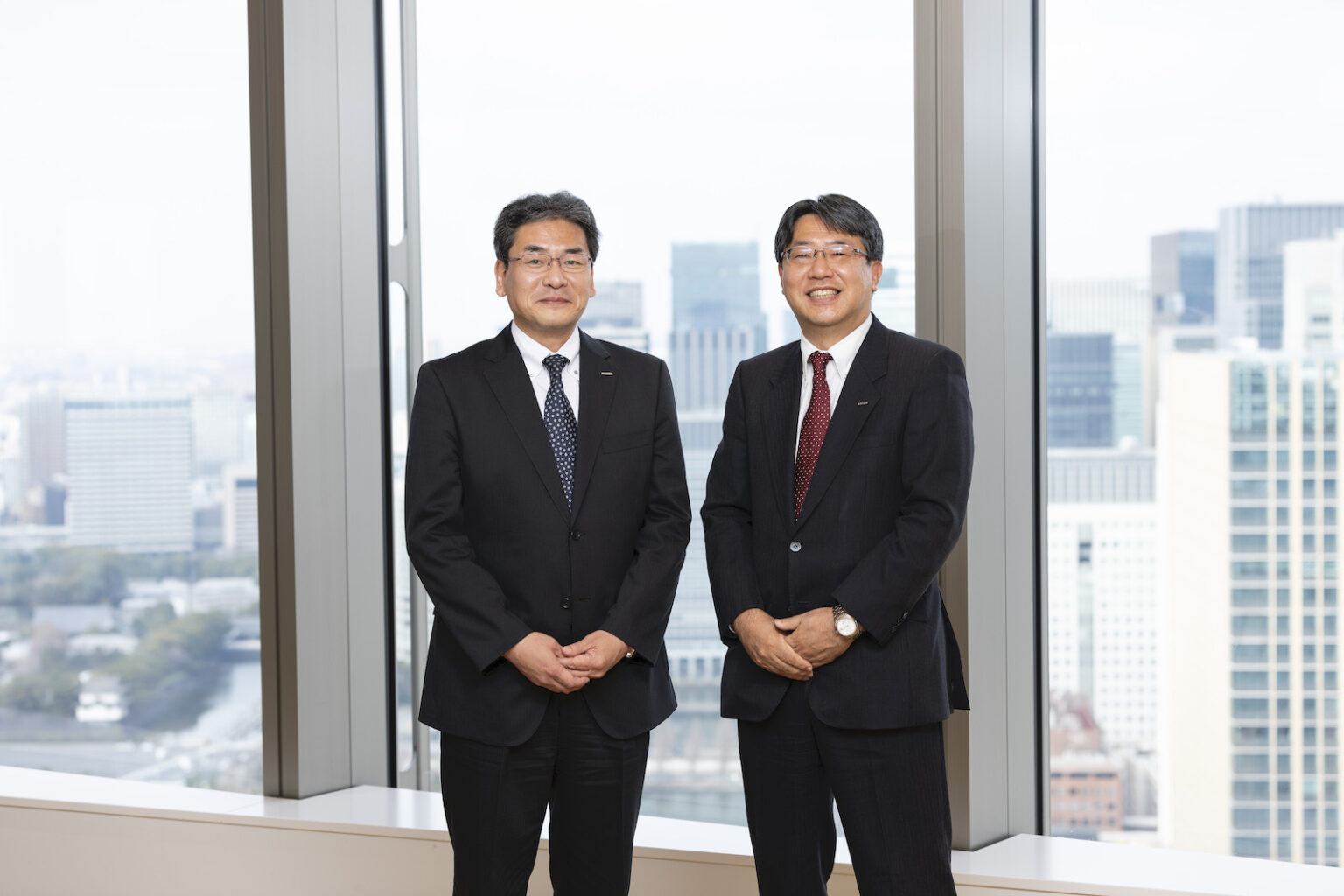
▲Katsuo Anzai, Senior General Manager, Mobility Materials Div., Performance Products SBU (right) / Shintato Oike, General Manager, Mobility Materials Planning & Coordination Dept., Planning & Coordination, Performance Products SBU (left)
The shift to EVs is progressing over three times faster than expected
Oike: Before talking about driving range, let me explain the status quo of the automotive industry, which has been experiencing a drastic change. Charts (1) and (2) below show the forecasts for automobile production as of September 2017 and February 2021 by powertrain type (power source). You can see that in just over three years, the estimated production of BEVs in 2030 (indicated in red) has increased about three times. BEVs are electric vehicles that run only on batteries. Hybrid vehicles (HVs) are not considered BEVs because they still utilize an engine. From this point on when I say “EVs” I will be referring to “BEVs.” At the Mobility Materials Division, we anticipate the shift to electrification, including fuel cell vehicles (FCVs), will advance even further than the forecast in chart (2).
EV batteries are much heavier than engines
Oike: Another important factor that we must consider when talking about a vehicle’s driving range is the difference in weight between EVs and internal combustion engine (ICE) vehicles. If you compare EVs and ICE vehicles by vehicle grade, such as mini vehicles, compact cars, sedans, or luxury cars, EVs are heavier. ICEs weigh from 100 to 200kg (220-440 pounds), while batteries generally weigh between 250 and 600kg (550-1,320 pounds). This weight difference will contribute to the total body weight of the vehicle.
We aim to extend driving range in terms of both mileage and battery durability
Anzai: Now that we’ve explained the premise, we will move on to the main point. Driving range has two meanings: the distance achieved on a single charge, and the total distance that a car can travel — in other words, durability.
Oike: On a single charge, for example, you can go from Tokyo to Osaka (about 500 km, or 310 miles) without refueling on an ordinary ICE vehicle. On the other hand, a typical EV may need to be charged along the way, since it uses electricity for functions other than driving as well, such as air conditioning and audio. On top of that, battery charging stations and other infrastructure has not yet been well established, and even with the infrastructure, charging the vehicle’s batteries would still take longer than refilling gasoline. However, if you increase battery capacity, the vehicle will become heavier, and this further increases the fuel cost, or in the case of EVs it would be considered “electricity cost.” As a result, increasing battery capacity does not necessarily increase driving range as you may expect. This poses a dilemma.
Anzai: From a durability viewpoint, EV batteries still degrade overtime, and do not last long. To make EVs widespread, we need to extend the driving range in terms of both mileage and battery durability. A longer driving range will directly increase the value of a car.
Asahi Kasei can contribute to a solution via weight reduction and thermal management technologies
Oike: There are numerous important factors to be considered in extending the driving range, such as weight, battery efficiency, tire rolling resistance, gear shifting efficiency, air resistance of the vehicle body, and drive efficiency. Various measures are being taken, but as a plastics supplier we believe we can contribute to a weight reduction of the vehicle body and thermal management of the battery.
◆ Weight reduction extends the total driving range
Oike: When we use the phrase “Weight Reduction with Plastics” we mean replacing metals with plastics. When iron is replaced by resin, in a simple comparison, the weight is reduced to one-fifth or one-sixth, as the specific gravity of iron is 7.8 compared to about 1.3 to 1.4 for plastics. Since the specific gravity of aluminum is 2.7, plastics can still reduce vehicle weight versus aluminum.
When the vehicle body is made lighter, all values of running resistance, such as air, acceleration, rolling, and gradient resistance will be reduced, and electricity cost efficiency will be improved overall. If a compact car body weighing more than one ton is reduced by 100kg, in general, its fuel efficiency improves by 1km per liter, and CO2 emissions fall by 15g per km. The impact of weight reduction on meeting environmental regulations is significant. For example, the portion of iron, which has a high specific gravity, the materials used for automobile production in the United States has been declining rapidly from nearly 80% in 2015.
◆ Thermal management of a battery can make it more durable and extend an EV’s driving range
Oike: There is an optimum environmental temperature for lithium-ion batteries used in EVs, and the batteries cannot showcase their true performance in high or low temperatures. If the surrounding parts of the batteries are replaced by plastics parts with excellent heat insulation and heat retention properties for thermal management at an optimum temperature, the batteries will achieve higher performance and efficiency, which will lead to extended battery life and improved durability.
Which Asahi Kasei engineering plastics contribute to the two ways of extending driving range?
Anzai: “Engineering plastics” are resins with different heat-resistant temperatures and levels of mechanical strength, rigidity, and chemical resistance from those of the general-purpose plastics used in day to day activities, such as plastic shopping bags. Asahi Kasei has been contributing to weight reduction with its three types of engineering plastics: XYRON, LEONA, and TENAC. Moreover, using these as materials, we have processed and developed new materials: SunForce and Continuous Fiber (Continuous Glass Fiber Reinforced Polyamide Resin).
◆ Asahi Kasei’s product family of three engineering plastics have shown great performance and have been improved over time
Oike: A battery case used to be a fairly large block of metal. If some of the parts are replaced by XYRON engineering plastic, the weight will be reduced by several kilograms. XYRON provides high barrier properties such as heat insulation and heat retention, so it has excellent heat management properties, which extends battery life.
●XYRONTM https://asahi-kasei-mobility.com/en/products/xyron/
Application examples: Battery pack (case), relay block, cell separator (battery component), fender, wheel cap, and other exterior parts
Oike: The water-cooled cooling pipe plays an important role in heat management. It has a length of several meters, and its weight can be significantly reduced if our LEONA engineering plastic is used. It also has excellent corrosion prevention and heat retention properties.
●LEONATM https://asahi-kasei-mobility.com/en/products/leona_sv104/
Application examples: High-voltage type cables, water-cooled cooling pipes, transmission equipment, shift levers, cylinder head covers, mirror bases, cup holders, etc.
Oike: TENAC is an engineering plastic that is extremely tough, wear resistant, and has good sliding properties, so it is often used for gears – in other words, it’s slippery. We also have an excellent product design lineup that features both of those properties.
●TENACTM https://asahi-kasei-mobility.com/en/products/tenac/
Application examples: Gear parts, interior (inside the door) handles, seatbelt press buttons, wiper gear units, window glass regulator parts, etc.
◆ New materials! The strong, foam beads of “SunForce” and the thin and sturdy “Continuous Fiber”
Anzai: SunForce is an engineering plastic that is foamed and expanded by five to ten times. It is very light and can be molded into various shapes. It has high strength and rigidity, excellent flame retardancy, heat resistance, heat insulation, and high dimensional accuracy, so it can be used as a component material or core material for thermal management, such as for battery parts.
●SunForceTM https://asahi-kasei-mobility.com/en/products/sunforce_bebh/
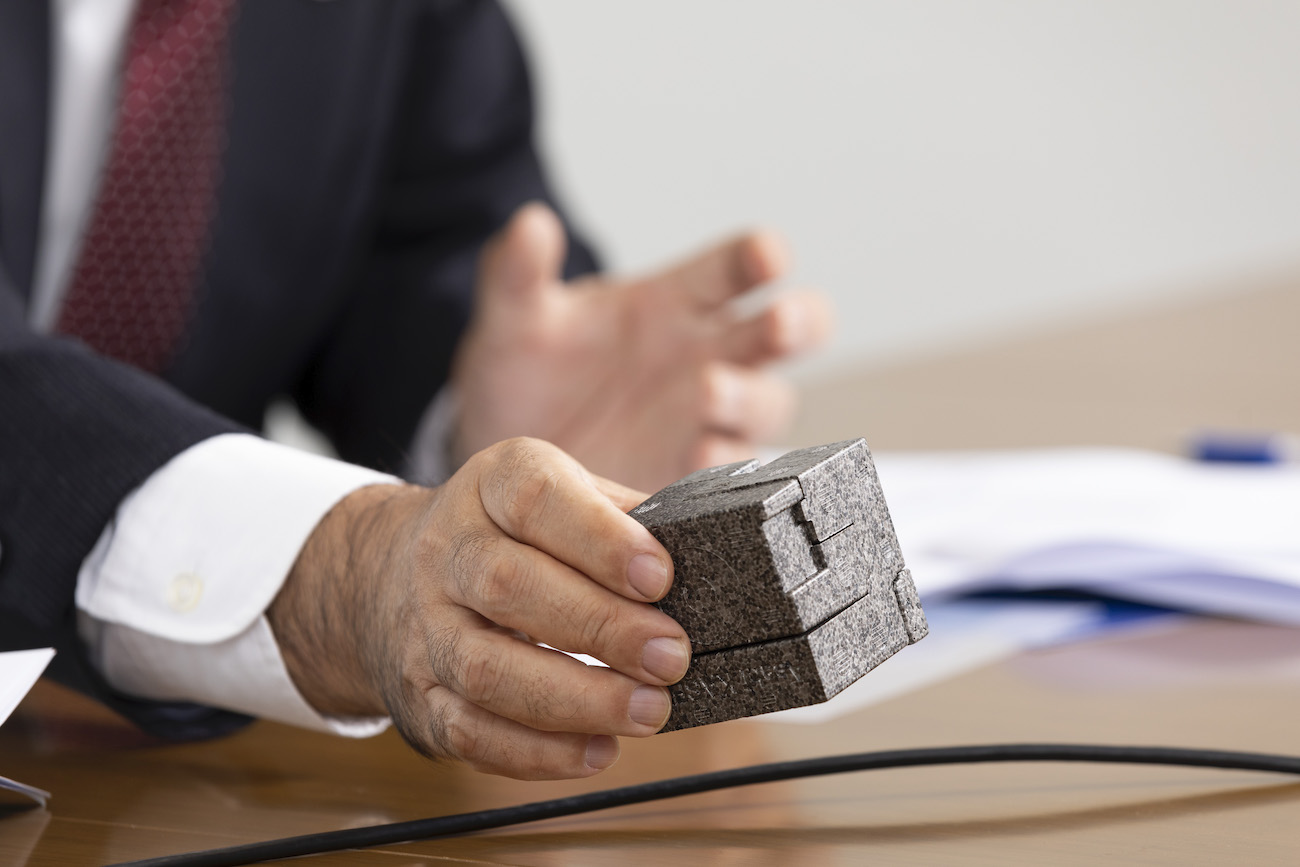
▲SunForce processed into blocks and colored. You will be surprised at how light it is when you hold it in your hand.
Anzai: Our continuous fiber is a state-of-the-art material developed by combining engineering plastic with woven glass fiber. Woven glass fiber is a composite with extremely high strength and gives excellent collision safety. Therefore, it is expected to be used in many different parts of a car, like the structural components of the car body itself. It is made into a sheet and can be processed into the shape of any part desired.
●Continuous Fiber (Continuous Glass Fiber Reinforced Polyamide Resin) https://asahi-kasei-mobility.com/en/products/continuous_glass_fiber/
Replacing metals with plastics to reduce the total cost of EV development
Oike: Replacing metals with plastics will reduce vehicle weight and improve thermal management, which will lead not only to a longer driving range but also total cost reductions. By making certain parts with plastics, they can provide safety and design comparable to those of metals at a lower price. Since plastics can be made into complex forms, you can combine or integrate multiple parts to reduce the number or size of the parts. If the number of parts is reduced, the assembly time at the factory can be shortened, and if the parts are made smaller, they can save space and increase the degree of freedom in design. When I think about what we are contributing, I feel that material and application development are the crux of Asahi Kasei’s engineering plastics.
Enhancing our proposals for products and solutions
Anzai: As the automobile industry is undergoing major changes, we are required to further increase the speed of development. In the past, we first asked Tier 1 suppliers (primary parts manufacturers) to make parts using our engineering plastic materials and then introduced them to carmakers. Recently, however, material suppliers like us have begun to collaborate directly with carmakers as well.
In addition to proposals to replace metals with the existing engineering plastics, we will focus on developing new materials and combining new and existing engineering plastics. Since we need to clearly show how to use new materials and what value they create, we make proposals using CAE (computer-aided simulation technology). We want to expand business opportunities in the mobility field by enhancing our product-oriented approach to proposals for manufacturing products and solutions, and then detecting and responding to new needs.
We are motivated to tackle the emerging challenges of a field in turmoil
Oike: The progress of introducing and adopting EVs are different in each country. European countries are quickly shifting to EVs because diesel vehicles do not meet their emission regulations. In addition, renewable energy use is being promoted and electricity costs are low in some countries. Meanwhile, China’s EV market has been growing the fastest in the world. The Mobility Materials Division is targeting markets for growth, including China, while staying aware of the trends in Europe, which has the most advanced automobile technologies.
How can we cope with the uncertain road ahead of us?
Anzai: We don’t think that EVs are the best in all aspects. We see fuel cell vehicles as promising, but they are still too expensive. We think the EV market will definitely expand on a global scale, but there are still uncertainties about the degree, as well as how much and how quickly it will grow. Being proactive and taking on challenges to create new values with new materials is important in times when the external environment, especially for the automotive industry, has been changing drastically.
Further details
『Asahi Kasei Engineering Plastics Information Comprehensive Site』
https://www.asahi-kasei-plastics.com/en/
Click here to contact us about Asahi Kasei’s products and usage examples.
This article was published on May 7th, 2021.