The Future of Sustainable Mobility
Contributing to a sustainable society through advanced engineering plastics
“XYRONTM,” contributing to the dissemination of EVs; and “TENACTM,” eliminating the need for painting
Mar 8, 2021
Since its foundation, Asahi Kasei has addressed social challenges as its mission, and developed new technologies and products to meet the demands of the times. One area in particular that continues to evolve at a rapid pace is “engineering plastics.” Engineering plastics are drawing worldwide attention as their various functions extend beyond the image of traditional resins, and they may contribute significantly to sustainable product development and business promotion. Focusing in particular on “XYRON,” and “TENAC,” Asahi Kasei’s engineering plastics that are expected to contribute to the mobility section, we interviewed Ippei Araya and Masayoshi Iwasa from related departments to discuss their appeal.
(* For the previous article, please see Case 01: ASACLEANTM)
Click here to contact us about Asahi Kasei’s products and usage examples.
Case 02: XYRONTM, an engineering plastic with diverse functions
“XYRON” is a general term for “modified PPE (polyphenylene ether) resins,” which Asahi Kasei started to manufacture and sell in 1979.We first took on a giant U.S. company that was leading the market at the time. Since then, we have pioneered a wide range of applications over more than 40 years. Like “ASACLEAN,” which was focused on in the previous article, in 2019 “XYRON” was selected as an “Environmental Contribution Product,” a title designating a sustainable product of the Asahi Kasei Group, and it now plays a key role in the dissemination of EVs. So what are its diverse functions and features…?
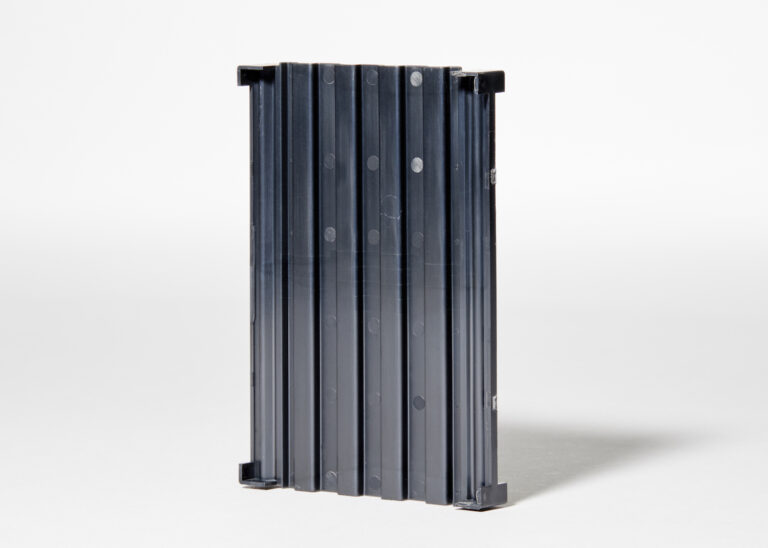
▲“XYRON,” contributing to light weight, flame retardancy, and high fluidity
Special characteristics of XYRON
Araya: With the lowest specific gravity of our range of engineering plastics, XYRON enables reduced resin content and light weight. XYRON is an environmentally friendly material that is halogen-free and flame retardant, does not burn easily, and does not contain halogen based substance that release toxic substances when disposed of. It is also resistant to impact. XYRON is resistant to acids, alkalis and electrolyte solutions, does not absorb water easily, and has high barrier properties. Furthermore, it has excellent dimensional stability. While many other plastics shrink or become slightly distorted after molding due to the ambient temperature or other factors, XYRON is finished precisely in accordance with the customer’s drawing.
Examples of products in which “XYRON” is used
Used in truck fenders, LiB end plate for EVs, and solar-energy-system components
Blending with other resins to create a diverse lineup of products
Araya: While XYRON has many superior properties as I have mentioned, many other features can be added through polymer blending with other resins. By using our “compatibilization” technology, which prevents polymers from separating, we can blend polymers to minimize their weaknesses, enhance their strengths, and add functions while maintaining the strengths of both polymers. For example, battery cases for hybrid vehicles need to be resistant to both gasoline and electrolyte solutions, and this requirement is satisfied by blending polypropylene, which is resistant to gasoline, with XYRON.
Reducing CO2 emissions, and improving battery life, leading to fuel efficiency and other advantages
Iwasa: Vehicle weight can be reduced simply by replacing metal parts with plastic parts. Among plastics, XYRON, with its low specific gravity, can also contribute to reduced CO2 emissions and reduced amount of resin used due to its light weight. Moreover, a battery case made of XYRON has high barrier properties thus improving battery life, while a fender made of XYRON reduces air resistance thus improving fuel efficiency.
* According to a survey by the Japan Aluminium Association, a 10% reduction in weight may lead to a 5 to 10% improvement in fuel efficiency.
* A lamp extension made of XYRON is 50% lighter than a conventional extension.
Continuous development work with an eye out for new applications
Araya: Demand for XYRON has expanded all around the world making it a primary revenue source for Asahi Kasei today, though there were difficult times when it was unprofitable. Without the persistent efforts made amid their situations by our predecessors with a mission to keep developing new things, XYRON would not have become what it is today.
Iwasa: Since XYRON is a material that can be used for a variety of purposes, sales, marketing, and technology departments all need to be capable of examining the possibilities of use for any and all purposes. We have cultivated new demand, always staying attentive to what developments and improvements customers are now addressing in various fields, what problems they face, and what the market trends are. It is no exaggeration to say that the history of XYRON is the history of our product development conducted together with our customers.
To be appreciated widely in the market and contribute to people’s lives and lifestyles
Araya: We aim to continue to contribute to sustainability by taking advantage of XYRON’s features. We want our customers to use the new materials we provide widely, for essential components, for environmentally friendly purposes, and in future growing fields— for example, in the further growing fields of electric vehicles and solar energy systems, for the development of products utilizing recycled materials that can contribute to the reduction of plastic waste, and—given XYRON’s excellent electrical characteristics—even in the information and communications field. We will strive to flexibly respond to the changes of the times and create our own markets in order to evolve our products and businesses to gain higher existence value.
◆ ◆ ◆
Case 03: TENACTM & TENACTM-C, tough engineering plastics
“TENAC” is a general term for “polyacetal (POM) resins” manufactured and sold by Asahi Kasei. As its name suggests, which is derived from the Latin word “tenax” meaning “tough,” TENAC is an extremely tough engineering plastic that comes in two types with different property trends: “homopolymer” and “copolymer.” There are a range of formulations for various purposes, such as the “metallic grade,” which can be used without painting. In what kind of products is it used in an environmentally friendly way? What is its future outlook..?
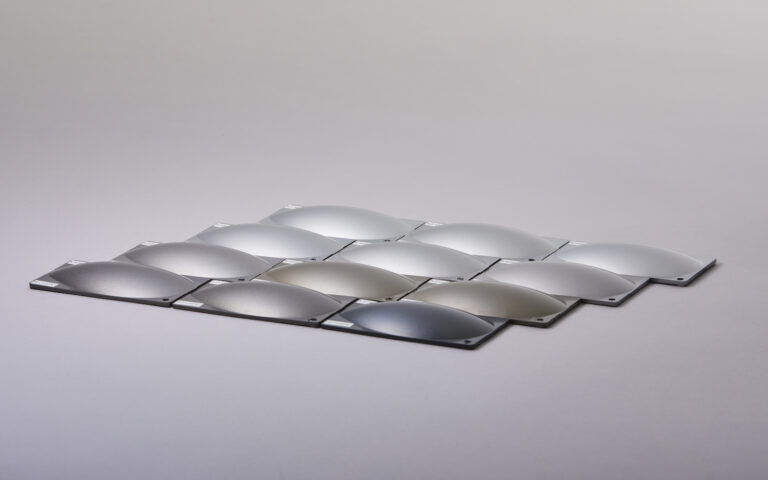
▲“TENAC,” with high designability and low VOC emissions, contributing to reduce cost and environmental load
Durability enabling long-term use—TENAC
A lightweight alternative to metal with added functions
Araya: TENAC is a tough plastic that has, among plastics, significantly high physical characteristics, such as high stiffness and high durability. Even if pressure is applied to it repeatedly or for a long period of time, TENAC will not become deformed or break easily.
For example, automobile gears, pulleys, components of window lifting and lowering devices, and other mechanical parts were conventionally made of metal. However, making them of TENAC will lead to weight reduction and fuel efficiency.
Moreover, metal gears become worn without the continuous application of lubricant. In contrast, since TENAC is self-lubricating, gears made of TENAC will not easily become worn. Furthermore, thanks to their excellent workability, TENAC parts can be manufactured in large quantities, leading to reduced production costs. As you can see, TENAC can not only replace metal but also provide functions that are unique to resin.
Examples of products in which “TENAC” is used
Used in gear components, seatbelt press buttons, fuel pump module etc.
The only company in the world that manufactures both homopolymers and copolymers—Asahi Kasei
Iwasa: TENAC is POM resin that come in two types according to its properties: “homopolymer” and “copolymer.” Asahi Kasei started to manufacture and sell the homopolymer type in 1972. This type has superior physical characteristics, such as greater stiffness and greater strength, and does not easily bend or become deformed. Later, Asahi Kasei started to manufacture and sell the copolymer type in 1985. This type is more easily handled because it contains a component that prevents resin from decomposing. It is resistant to chemicals, and is less susceptible to shrinkage.
Araya: Asahi Kasei is the only company in the world that manufactures and sells both types. We are able to take advantage of the strengths of both types and offer the best option to our customers.
“Metallic grade” possess both designability and durability
Iwasa: TENAC comes in a variety of grades for many purposes. It used to be said that a metallic colored resin was difficult to achieve, but the metallic grade has a beautiful metallic color. This grade is used for the inner handles of automobiles, parts that need to be both strong and designable. Since TENAC is resistant to chemicals, people don’t need to worry about damaging the material by repeatedly applying pressure with their hands covered in cosmetics containing organic solvents or food oils.
Examples of products in which the metallic grade is used
Inner handles etc. “For parts with a streamlined shape or any other shape that is difficult to process, using metal would be costly. Moreover, metal feels cold when we touch it in a cold environment. However, when we touch TENAC, it feels rather warm thanks to its low thermal conductivity. We will develop more shiny and more metallic colors so that we can offer a wider range of colors to our customers.”
“Metallic grade” eliminates painting process to reduce the environmental load
Araya: Eliminating the painting process by using the metallic grade of TENAC enables the reduction of (i) organic compounds in painting materials, (ii) waste liquid, bad odors, and VOCs (formaldehyde) generated in the course of the painting process, and (iii) waste of materials generated in the painting process, leading to reduced environmental load and workload on workers. Moreover, using the metallic grade eliminates non-uniformity, pinholes or any other nonconformities in the painting surface, which usually occur in the course of the painting process. Customer feedback indicates that total costs can be reduced by about half.
Our persistent predecessors and our customers made TENAC what it is today
Araya: There are only two companies in the world that manufacture homopolymers. I heard that, as was the case with XYRON, when TENAC was launched, a giant U.S. company dominated the market at the time, and our predecessors faced considerable difficulties. Repeating trial production to improve quality and performance, offering trial products to customers for use, and if they say “no,” repeating the production process again and again— such persistent predecessors who never gave up and kept on making improvements, and the customers who gave them the opportunities and support, led to what TENAC is today.
Contributing to a sustainable future through proactive material development
Iwasa: Our aim for TENAC is to continue to develop applications for evolving mobility sector and to pursue further improvements, thereby contributing to the environment. As well as the automotive field, we will utilize the uniqueness of TENAC in the robot, MIM,* and medical treatment fields and exploit new uses and markets. To this end, we will keep ourselves open to market trends and grasp customer needs in advance so that we can develop new materials as quickly as possible.
* Abbreviation for “metal injection molding” A new technique whereby resin is mixed in the course of metal molding to create a precise, complex shape that is impossible to create with just metal.
Future of resin—
Responsibility for recycling technology, hints of ideas from movies
Araya: In order to change the world now, we, as chemical manufacturers, have an extremely important role to play in the field of plastics (resins). With respect to the problem of plastic waste, we ourselves have a mission to improve our technology to develop products that do not easily become waste or can be disposed of easily, and also to conduct recycling in a stable manner. Chemical manufacturers also have to deal with the challenge of functional deterioration or color change of materials caused by recycling. These are extremely demanding tasks, but they constitute our raison d’etre. By addressing these tasks, we can contribute to the world.
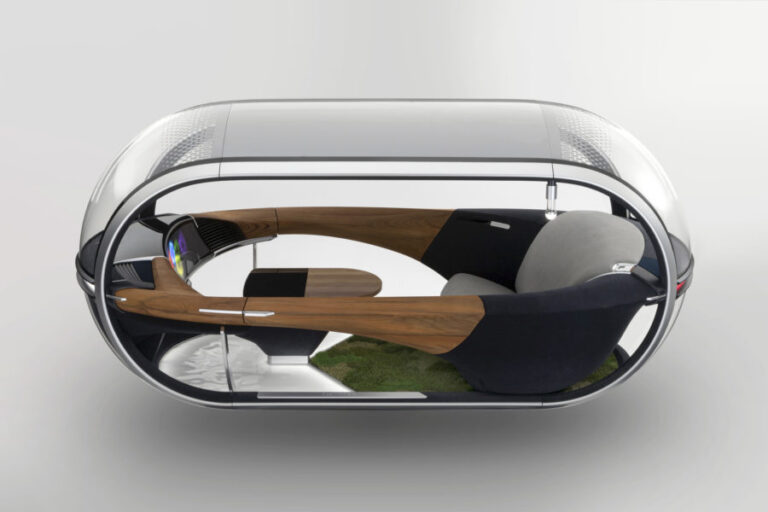
▲“AKXY POD,” a proposal for comfortable in-vehicle spaces of the future. Comprising a variety of Asahi Kasei fiber products, plastics and sensors, it embodies the company’s concept for the future of passenger comfort, safety and security inside vehicles. For details, click here.
Iwasa: Collecting information on trends from various documents and market opinions, we sometimes consider using our engineering plastics, for example, in flying cars.
Araya: We’re so hooked on science fiction movies, aren’t we? (laughs) Science fiction movies are full of ideas. We often talk about the technologies and opportunities derived from them.
Further details
『Asahi Kasei Engineering Plastics Information Comprehensive Site』
https://www.asahi-kasei-plastics.com/en/
Click here to contact us about Asahi Kasei’s products and usage examples.
This article was published on May 8th, 2021.