Asahi Kasei’s new technology for chemically extracting polyamide 66 from scrap vehicles
As the world aims for a sustainable circular economy*1, the waste and greenhouse gas (GHG) emissions*2 from vehicles are still significant, making them an urgent social issue. The vehicles in demand today have a low environmental impact and high recyclability, not only when driven but across their entire life cycle, from design and production to disposal and recovery. Of particular note is that in July 2023, the European Commission announced an amendment to the End-of-Life Vehicles (ELV) Directive, which targets recycled materials being used for 25% or more of the plastics required for new vehicle production, of which at least 25% will be sourced from scrap vehicles.
For a long time, Asahi Kasei has been developing high-performance plastics that contribute to EVs and other next-generation vehicles, and it has also increased environmental considerations of materials. Among these considerations are chemical recycling and bioplastics, which are expected to gain popularity as technologies that support automotive components. In Part 1 of this report, we will hear from Dr. Yasuhisa Ichihashi, who is aiming to implement efficient chemical recycling of polyamide 66 (“PA66”; LEONATM in Asahi Kasei’s product line), about topics including the roadmap for wide deployment and overseas trends.
*1: United Nations Environment Programme (UNEP) International Resource Panel (2016), Report on Resource Efficiency.
*2: Environmental White Paper (2023)
For more on Asahi Kasei’s products, their uses, and technology, please contact us using this form.
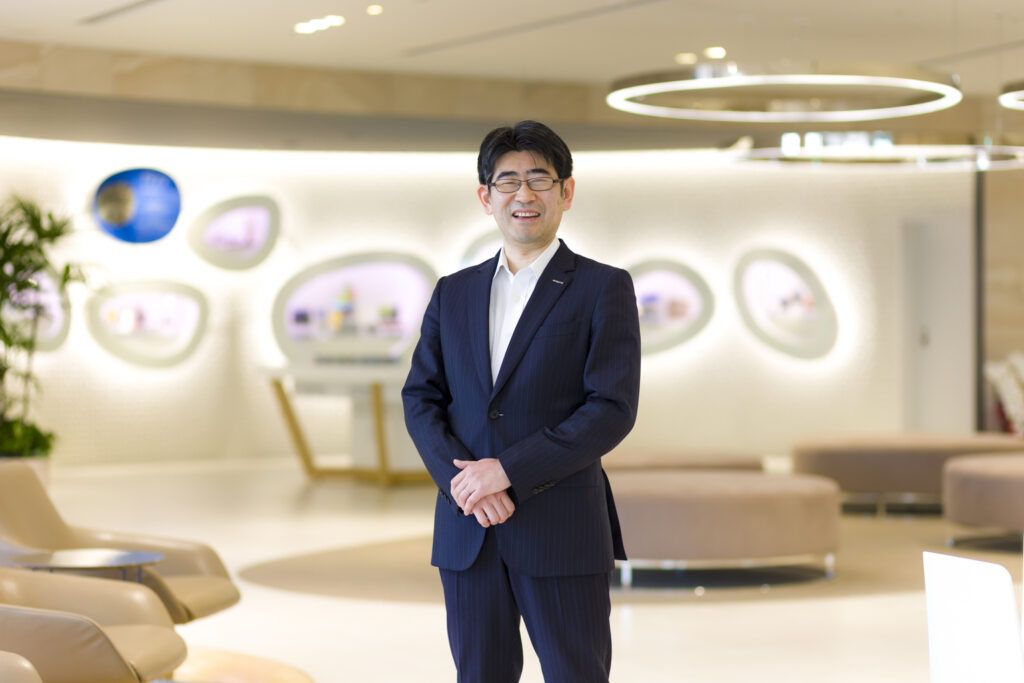
▲Yasuhisa Ichihashi, Ph. D., Advanced Technology Development Dept.
Purification from waste materials at the molecular level to cleanly extract plastics
Ichihashi: “There are three ways to reduce the environmental impact of the plastics manufacturing process: mechanical recycling, chemical recycling, and the use of bioplastics. The first two are recycling technologies, each with its own advantages and disadvantages. First, mechanical recycling is the use of waste materials such as polymers. On the plus side, this is a relatively inexpensive and easy operation to start, and it requires relatively little energy for the recycling process. However, it is difficult to completely remove impurities and foreign substances, and the physical properties will inevitably deteriorate, so circulating materials multiple times is challenging.
“As the name suggests, bioplastics are plastics made from biomass (organic resources, such as plants). While replacing the petroleum with biomass for the raw materials allows for production of high-quality materials with a quality equivalent to that of virgin materials, mass production does have its issues. A separate team from Asahi Kasei is currently working on development of this technology.
“Then, there is chemical recycling. As material is purified at the molecular level, even dirty material and composites from scrap cars can be cleanly extracted. In theory, this method can produce the same physical properties as 100% virgin material, and materials can be used multiple times for quality, high-performance vehicle parts. These are its great advantages. To date, however, the separation and purification processes have been somewhat energy-intensive, making this method less effective than mechanical recycling at reducing GHG emissions. Initial investments in plant construction have also been costly.”
Using microwaves to achieve chemical recycling of PA66 with low environmental impact
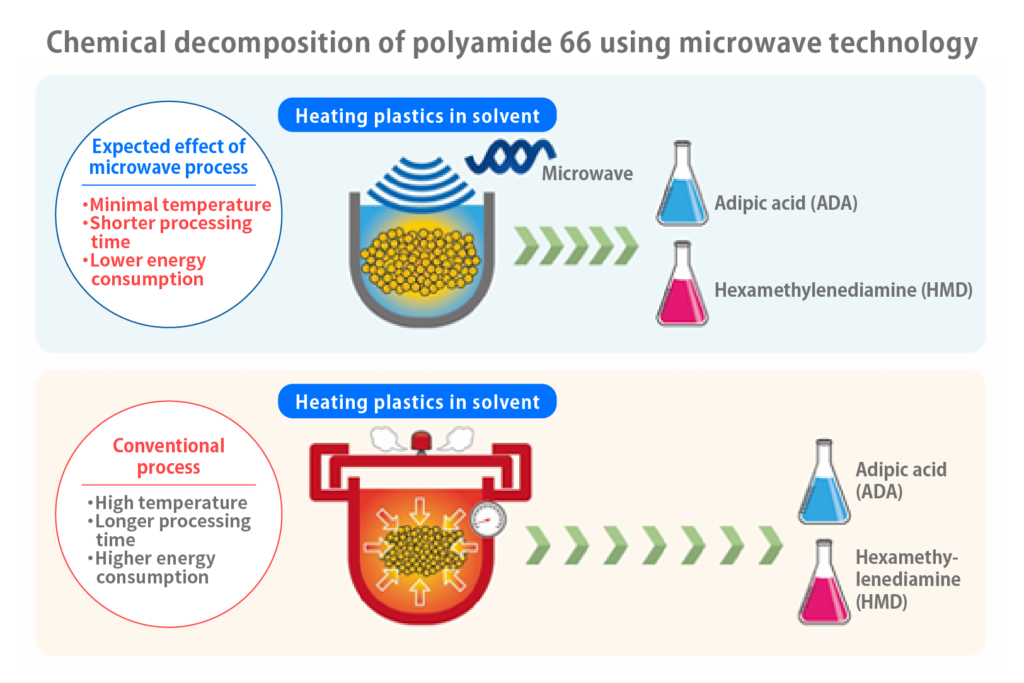
▲illustration of polyamide 66 decomposition using microwaves
Ichihashi: “The chemical recycling we have now developed is a recycling technique for high-performance plastics PA66, plastics used in various auto parts, such as airbags and radiator tanks. The PA66 is decomposed into adipic acid (ADA) and hexamethylenediamine (HMD) by depolymerization. One characteristic of this process is the use of microwaves to supply the thermal energy. Since 2021, we have been working on exploration themes and have been developing technology with Microwave Chemical Co., Ltd., which has the technology to industrialize microwaves.
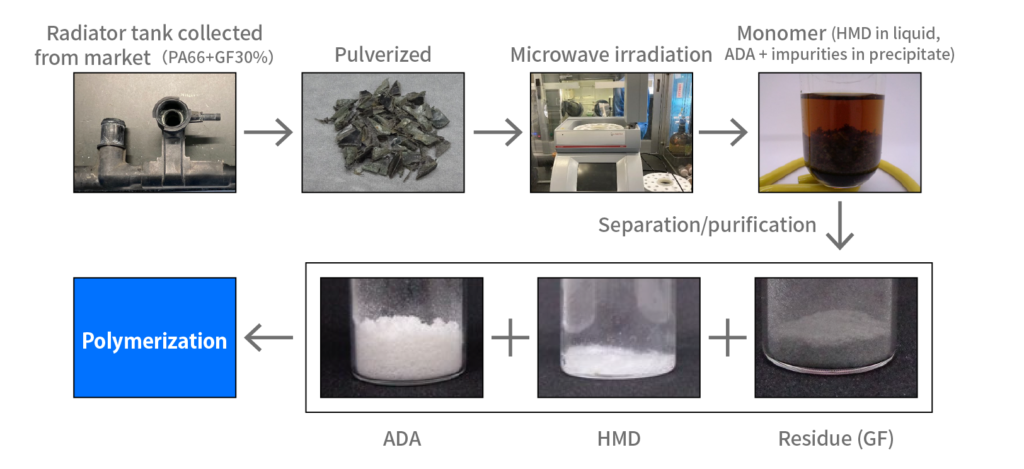
▲PA66 chemical recycling process from radiator
“With our technology, energy can generally be applied directly to a target object using microwaves, based on the same principles as in a microwave oven. It also involves fewer processes, giving it the potential to reduce energy consumption compared to existing heating processes. If powered using renewable energy for electricity, it could further reduce GHG emissions and recycle high-quality, high-performance PA66 plastics efficiently. For purification, we are considering a more efficient process by utilizing technology cultivated in various Asahi Kasei operations to date. About 70% of PA66 is bound for vehicle use. Asahi Kasei is one of the leading companies in domestic and Asian markets, with aspirations of taking the lead in this field.”
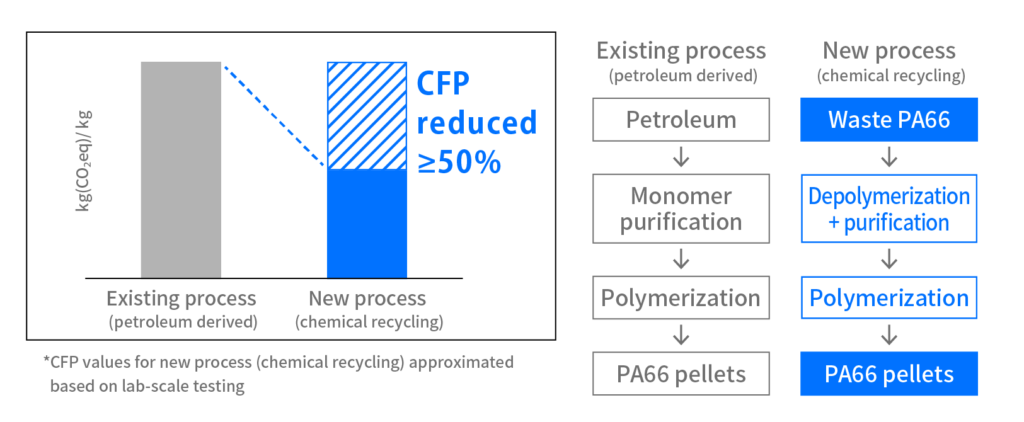
▲Comparison of carbon footprints (CFP: CO2 emissions) for Asahi Kasei PA66 chemical recycling and existing process
Making circular supply chain partners through co-creation and collaboration
Ichihashi: “In parallel with development of this technology, we are also looking for customers who recognize the added value in chemical recycling. To establish the viability of this operation, it will be essential to build a series of platforms, from collecting waste polyamide to getting the processed and restored products to users and, from there, repeating the cycle. Asahi Kasei cannot do this alone, so we are making partnerships.
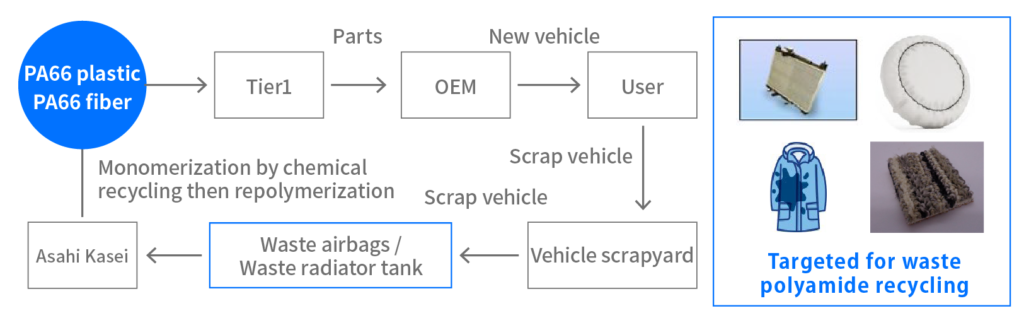
▲Platform for wide deployment of chemical recycling
“In 2020, Asahi Kasei launched BLUE Plastics, a digital platform for making the plastics recycling loop more transparent. It is also a participant in the Cabinet Office’s Cross-ministerial Strategic Innovation Promotion Program (SIP) “Building a Circular Economy System” with Nomura Research Institute Co., Ltd. to discuss defining requirements for PLA-NETJ, (Plastic Networking for Environmental Transformation Japan). As part of this, chemical recycling of PA66 is selected as a field for demonstration testing and information sharing. In the demonstration tests, the plan is to create a chemical recycling platform together with end-users such as vechicle scrapyards, parts manufacturers, and automakers (OEMs).
“Even if each company possesses the technology to do so, no recycling operations will proceed unless profitable. Thus, we want to create a system for commercialization of the process which coordinates interests and other factors. Last year in 2023, we issued press releases and were active on the exhibition and academic conference circuit to spread the word. As a result, we have had contact from more end-users. We’ve also had requests from potential customers to let them know when samples of chemically recycled PA66 are available.”
The trigger for advancing into a sustainable world is a clear statement of intent
Ichihashi: Up until I was assigned to this research in 2021, I was stationed in Düsseldorf at Asahi Kasei Europe (AKEU). Already at that point, the impression locally was that automaker executives were clearly stating specific figures for what percent of recycled materials are to be used by when, which has sent everyone scrambling to find recycled materials to meet those targets. It felt like many companies wanted to use sustainable products as a corporate course of action prior to any regulations being decided. The policy and perceptions were that recycling would be promoted as a new industry. Conversely, strategic aspects in the future may exclude areas where sustainable products are not used.
“In terms of global trends in chemical recycling, PA66 is still scarce, but polyamide 6 (PA6) is being actively promoted by overseas manufacturers. Increasingly more major apparel manufacturers are already adopting PA6. We have also had apparel manufacturers tell us that they would happily use chemically recycled PA66 materials, so we sense the demand. The apparel industry has a shorter consumption cycle than the automotive industry, so new proposals can reach fruition fairly quickly. It seems that they are a bit ahead of the curve. With the European Union (EU) agreement in December 2023 to revise the Ecodesign Directive and ban apparel companies from disposing of unsold garments, this trend is likely to accelerate. With so many of the functional materials in clothing, such as those for water repellency and waterproofing, being composite materials, I expect that the ability of chemical recycling to separate materials neatly will make it even more prevalent in the future.”
Social contributions with the theme of resource recycling
Ichihashi: “Currently, we are working on the technical aspects of scaling up in order to commercialize chemical recycling. Working with Microwave Chemical Co., Ltd., bench equipment is planned for launch in fiscal 2024, with trial runs performed through the end of the year. In fiscal 2025, that equipment will be used to collect various data and identify issues. The company plans to verify costs to determine whether commercialization will be profitable and whether to actually proceed with operations and plant construction by the end of fiscal 2025. If the green light is given, the plant will be completed and production will begin in fiscal 2027 at the earliest. Japan will be the first priority for the plant location, expanding to global customers in Europe and elsewhere in the future by licensing the technology.
“We are currently specializing in polyamide 66, but in the future, for example, we could team up with chemical manufacturers and OEMs to propose and create a well-oiled system to efficiently collect other materials used in vehicles throughout society. We want to contribute to society with the theme of resource recycling.”
*Chemical recycling of polyamide PA66:
https://www.asahi-kasei.com/news/2023/e230427.html
In Part 2, we will introduce bioplastics technologies that Asahi Kasei are pursuing to achieve a circular economy.
For more on Asahi Kasei’s products, their uses, and technology, please contact us using this form.
This article was published on June 12, 2024.