Creating basic chemicals: New technology for creating high-performance recyclable plastics from biomass
In Part 2, we introduce bioplastics technology from Asahi Kasei as an environmentally-friendly solution to the current demands across the complete automotive life cycle, from production to recovery. Bioplastics refers to plastics made from biomass rather than petroleum. Given the potential to significantly reduce CO2 emissions in the material production phase, R&D efforts with regard to bioplastics are underway around the world. However, there have been several challenges in the proliferation of this technology, such as concerns about quality and stable supply. Utilizing research started 10 years earlier, Asahi Kasei is working to develop technology that will culminate in recyclable, plant-based bioplastics with general-use applications in automotive parts. This technology is expected to enable the transition to a circular economy and supply sustainable materials that help to promote a decarbonized society. Here, we will hear from Hiroshi Kakihira, who plays a central role in business development, about the characteristics of bioplastics and the challenges regarding its mass production.
For more on Asahi Kasei’s products, their uses, and technology, please contact us using this form.
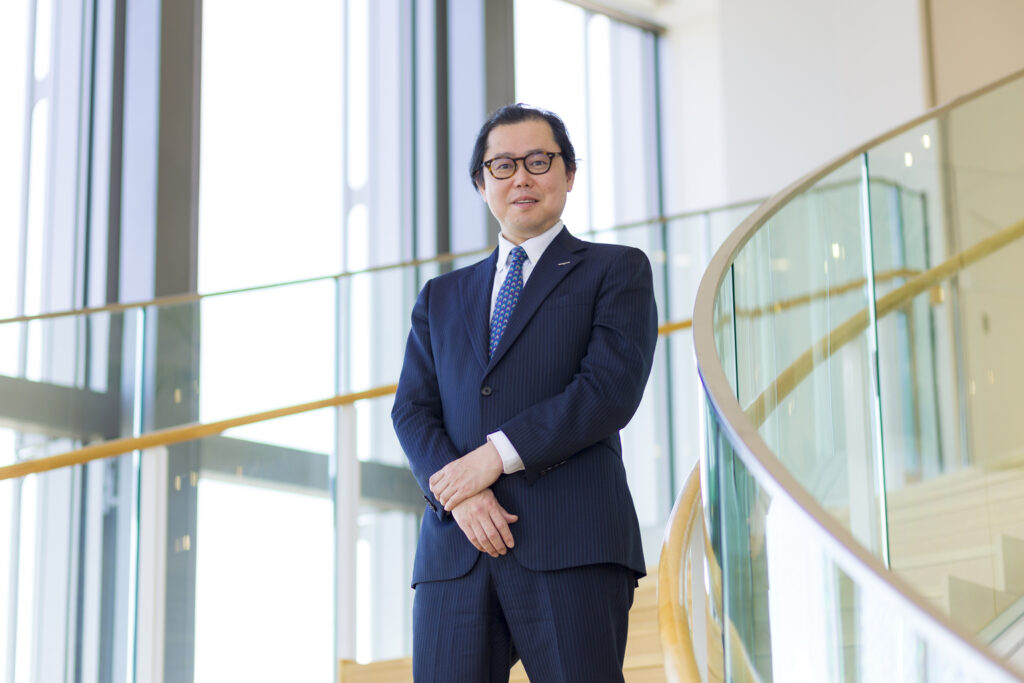
▲Hiroshi Kakihira, Green Solution Project, General Manager
Producing high-performance automotive plastics from plants and other sources
Kakihira: “Bioplastics are plastics made from organic resources such as plants, also called biomass. Bioplastics come in various types, but the most commonly known is probably biodegradable plastic. Placed in soil under the right conditions, these plastics will decompose. Their shortcoming, however, is that they are not readily recyclable for reuse. There are also bioplastics made from new basic raw materials obtained by fermenting sugars in what are called fermentation methods. At Asahi Kasei, we have developed a technology to chemically process bioethanol and create basic chemicals for use as raw materials for plastics. Ethanol is most commonly made using raw sugarcane and corn. It can also be made from inedible parts such as dregs, cores, leaves, or other agricultural residue.
This technology is designed to emit less CO2 than existing processes. Furthermore, unlike biodegradable plastics and new plastics made only from fermentation methods, our technique enables us to create engineering plastics with a performance and quality no different than those of existing engineering plastics.”
Creating a variety of bioplastic products using existing equipment
Kakihira: “This technology allows us to make plastics with the same usability as before simply by swapping out petroleum with biomass for the raw materials. The manufacturing process is the same, mixing various materials and molding them as before, so the existing equipment can be applied as-is. We can mix petroleum- and biomass-based plastics to make products. This bioplastic also has a major advantage in that it can be recycled.
In fact, Asahi Kasei once conducted some research and development on biomaterials, some 10 years ago. The technology was demonstrated but ultimately shelved as at the time, ethanol was expensive and bioplastics were not in demand. Demand in Japan has since increased for products made with sustainable materials, and so R&D was resumed in the spring of 2021. Based on the accumulated data, we are reviewing the processes for catalysts and other elements and have entered the plant design phase. With our storied past track record, the development period should be quite short”.
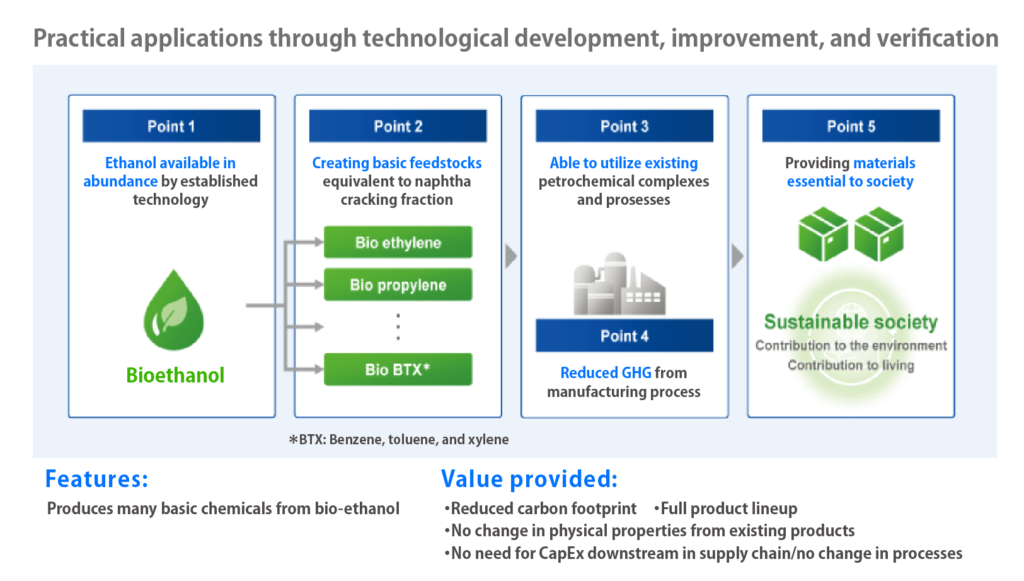
▲Asahi Kasei’s solution for creating basic chemicals from bio-ethanol
“In addition, Asahi Kasei’s petrochemical technologies cultivated over more than 50 years, for areas such as catalysts and process design, come in quite useful for this newly developed technology. Research on efficient petroleum use has been applied to the technology to master use of biomass-based raw materials.”
Contemplating with potential customers on how to convey new value to consumers
Kakihira: “For mass production, we are considering Japan, South Korea, Thailand and other Asian countries as candidates for plant construction. We want to gradually ramp up production capacity as demand increases. At the same time, we will advance with licensing. Concurrent with plant design, we have to think about how to build the entire business, from procurement of raw materials to securing customers. For sourcing raw materials, we are in talks with ethanol suppliers. Sugarcane-derived ethanol is produced globally and is currently often mixed with gasoline for use as fuel. However, as EVs become more widespread and demand for gasoline decreases, we believe that it can be utilized for bioplastics.
We are searching for suppliers of raw material for bioplastics, both in Japan and abroad in Europe and the United States. Typically, automotive OEMs have the power to make decisions on adoption of sustainable biomaterials. We meet with OEMs to discuss how to get them to adopt bioplastics and how to communicate their value to consumers. Many are surprised to hear about the variety of plastics that can be made from bioethanol.”
Europe is the driving force, and Japan must develop bio-certification
Kakihira: “Consumers overseas, especially those in Europe, have long sought to use products made with sustainable materials, and bioplastics are attracting attention as one of the solutions. Almost 20 years ago now, back in 2005, the EU introduced their Emissions Trading System (EU-ETS) to encourage energy and other consumer industries to curb their GHG emissions. I was stationed at Asahi Kasei Europe in Germany up until 2021. Back then, we were already fielding questions from European customers on topics such as how much CO2 a material emits, or how to create a roadmap for recycling raw materials and replacing them with sustainable materials in the future. Japan has finally started to change in the last few years.
In Japan, however, in many cases, even if the interest in bioplastics is there, the high price compared to existing plastics is still a delimiting factor. Price largely depends on the raw materials, so as volumes increase with more widespread use in the future, the plants will increase in size and produce economies of scale. That should make things somewhat more affordable.
While price is also a bottleneck, for the Japan market, another major hurdle is the lack of awareness of the mass balance approach. Put simply, in the mass balance approach, if a total of 100 tons of raw materials have 5 tons replaced with bio-based raw materials, instead of the product being certified as 5% bio-based overall, 5 tons of product is certified as 100% bio-based. With this system, rather than increasing the price of the product across the board, end-users receptive to the value of biomaterials can be supplied with 100% bio-certified products. Unlike in Europe, however, the Japanese understanding is still advanced only upstream in the value chain, in the petrochemical sector.”
Achieving a recycling-based society with both recycled and bio-based products
Kakihira: “In the future, we feel that the better proposal for us in plastic automotive parts is to first focus on recycling, and then replace materials that are not readily recyclable with bioplastics. For example, the urethanes used in synthetic leather, interior surface finishing, paints, adhesives, and other applications are hard to recycle. Using bio-based materials in parts that cannot be recycled will reduce CO2 emissions, so we may push for using bioplastics in the future.
For bioplastics applications outside the automotive sector, polyethylene made from sugarcane-derived ethanol is processed into plastic bags and sold in Japan. In addition, when recycling PET bottles for beverages and polyester clothing fiber, it is impossible to recover 100% of the material, leaving a certain amount of material shortfall. It would be desirable to use bioplastic for that shortage in the future.”
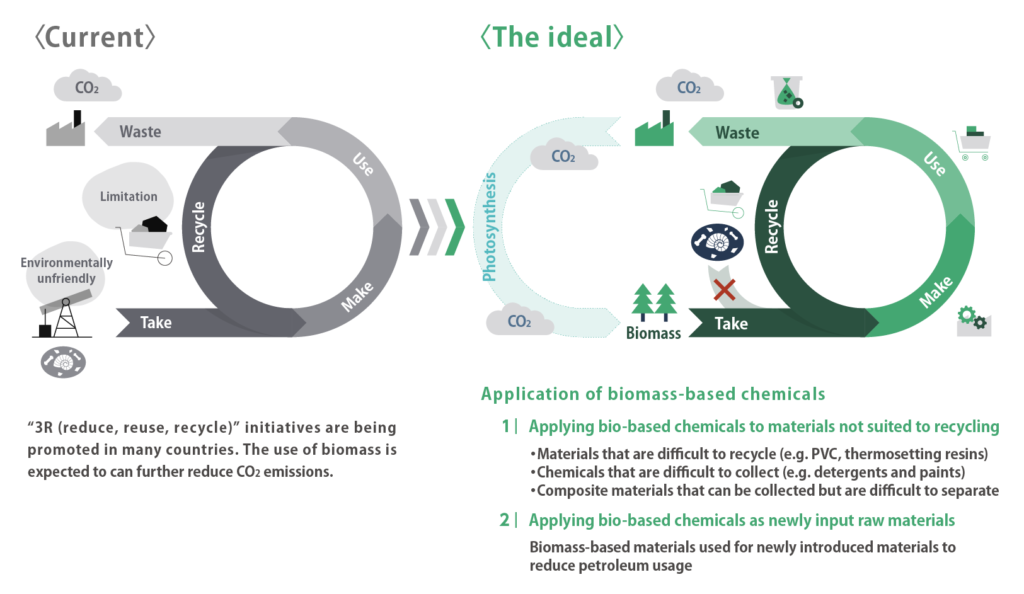
▲Role of bioplastics in the transition to a circular economy
“With the technology we are developing, we can make almost all so-called basic chemicals from bioethanol. It has the potential to transform everything that has been made from petroleum into bio-based products. It might still be quite a long way off in the future, but it would be great if all plastics and chemicals, not only in Japan but the whole world over, could eventually be recycled and bio-based. With both recycling and biotechnology, we could achieve a truly circular economy.”
“Contributing to the circular economy: more bio-based auto parts” : https://ak-green-solution.com/biobased_materials/en/
Since its founding, Asahi Kasei has proposed many new values to society, with the Group’s mission of contributing to the lives and livelihoods of people around the world. New technologies for chemical recycling and bioplastics manufactured from basic chemicals draw on the diverse knowledge that Asahi Kasei has cultivated over its many years in business. There is only so much we can do on our own, however. Social issues are increasingly intertwined, and solving them requires coordination and collaboration across industries and other traditional boundaries. We hope you will join us in contemplation and team up to achieve sustainable vehicles and a transition to a circular economy.
For more on Asahi Kasei’s products, their uses, and technology, please contact us using this form.
This article was published on October 17, 2024.